Jak powstaje klinkier?
Wygląd klinkieru nie zmienił się zbytnio na przestrzeni wieków, jednak metody jego wytwarzania są zdecydowanie inne. Zapraszamy na wędrówkę przez wieki, lub jak kto woli - wirtualny spacer po fabryce klinkieru.
Najważniejsza jest glina
Od czasów manufakturowego wytwarzania w średniowieczu cegły gotyckiej do technologii wykorzystywanych obecnie, pierwszym etapem produkcji cegły jest pozyskanie odpowiedniego surowca.
W średniowieczu glinę na potrzeby produkcji pozyskiwano łopatami i składowano w dużych dołach. Podczas składowania glinę mieszano z wodą, dodawano dodatki ułatwiające suszenie. Surowiec mieszano przy użyciu dwóch metod depcząc ją lub używając kieratów napędzanych przez zwierzęta.
Procesy wydobywcze, jak i prosty przerób masy, były wykonywane z największą starannością. Wiedziano wówczas, iż selektywne wydobywanie złóż gwarantuje poprawny przebieg całego procesu produkcji. Nauczono się rozróżniać rodzaje glin i śledzić proces przetwórczy w zależności od dodawanych dodatków występujących naturalnie w złożu i dodawanych celowo jako substancje pomagające w procesie suszenia. Przygotowana masa formierska miała dużą zawartość wody, formowane w późniejszych etapach cegły były duże i ciężkie.
Obecnie złoża eksploatowane są mniej wybiórczo, co jest skutkiem produkcji wielkoseryjnej i wykorzystywania do eksploatacji złóż dużych kombajnów i koparek. Surowiec w celu ujednorodnienia trafia na hałdy a dopiero w kolejnym etapie do przerobu wstępnego masy. Gliny po przejściu przez kołogniot, są wzbogacone o precyzyjnie dobrane dodatki piasku, i/lub szamotu. Następnie są transportowane do dołowników, skąd przy użyciu koparek wielonaczyniowych wybierane są i taśmowo podawane do przecieraków. W przecierakach dodawana jest woda w niewielkich ilościach.
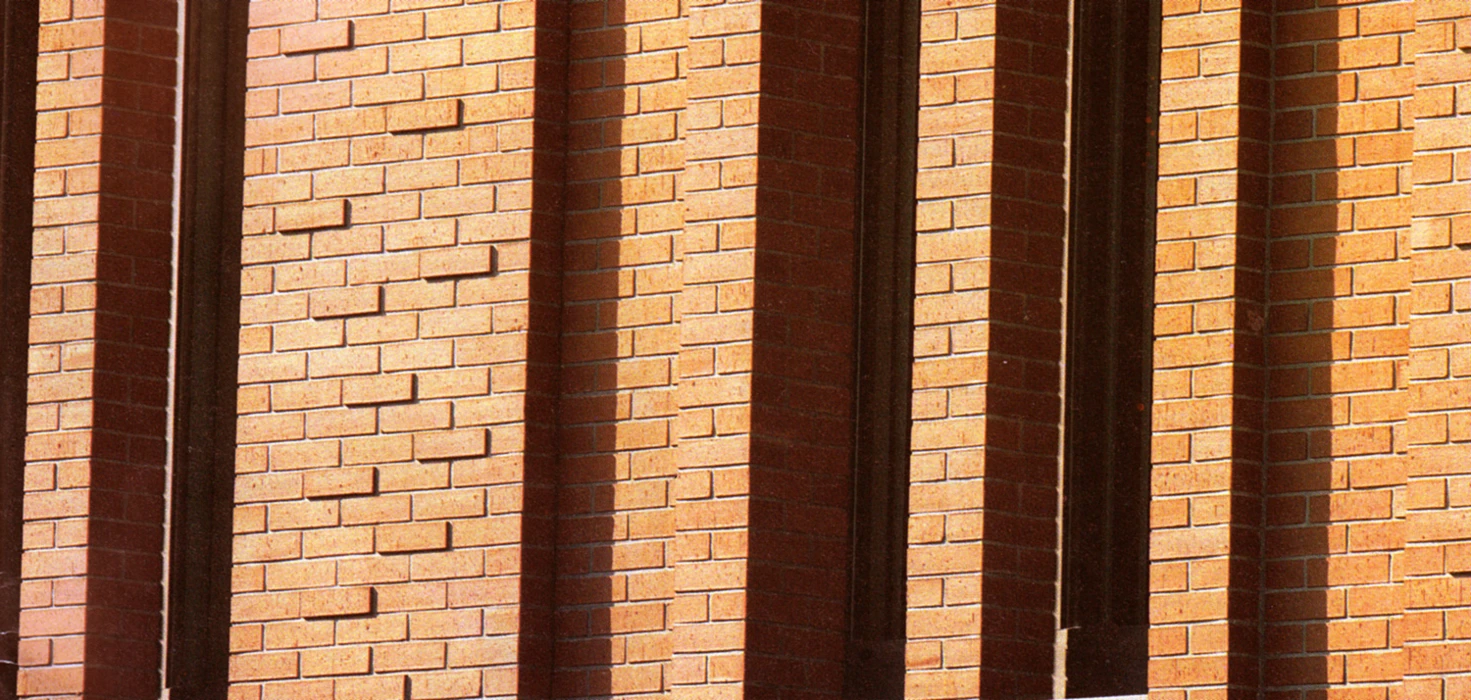
Automatyczny strycharz
Dzisiaj etap przygotowania i formowania masy prowadzi się przy użyciu jak najmniejszej ilości wody, którą przed procesem wypału, należy odprowadzić z cegły. Wiąże się to ze znacznymi nakładami czasu i kosztów suszenia. Obecnie cegła jest dokładnie mierzona. Po procesie wypału musi być równa i odpowiadać wysokim standardom wymiarowym. Dlatego tak ważne jest dodawanie niewielkiej ilości wody i monitorowanie stałości przygotowania mieszanki.
Dawniej cegłę formowano w drewnianych ramach. Ubijano ją młotkiem, a nadmiar wystający poza obrzeża ramki zbierano patykiem lub drewnianą listwą (strychulcem).
Dzisiejsi prasiści obsługujący automatyczne prasy próżniowe o wysokich wydajnościach takich firm jak Haendle lub Rieter to dawniejsi strycharze. Wyformowana przez nich cegła to palcówka. Nazwę taką cegła gotycka przyjęła ze względu na technikę formowania. Podczas zbierania nadmiaru gliny z ramki palce formiarza odciskały się w mocno wilgotnej masie.
Dzisiaj podobną metodę formowania stosuje się w produkcji cegieł ręcznie formowanych. Galety masy trafiają do skrzynek formierskich, pokrytych piaskiem, aby zapobiec przywieraniu gliny do ramy i nadać cegłom odpowiedni wygląd. Obecne prasy uzupełniane są gliną około 24 razy na minutę. Charakterystyczne „fałdy” na wyformowanych wyrobach, powstające na skutek wtłoczenia masy w formę, zdobią lica dzisiejszych cegieł ręcznie formowanych i nadają im niepowtarzalny wygląd. Proces formowania dzisiejszych cegieł „ręcznie formowanych” jest najbliższy technice używanej w czasach wcześniejszych.
Z tym, że proces schnięcia wyrobów trwa około 2 dni, a cegła traci około 1 litra wody i zmniejsza swoje wymiary o około 8%.
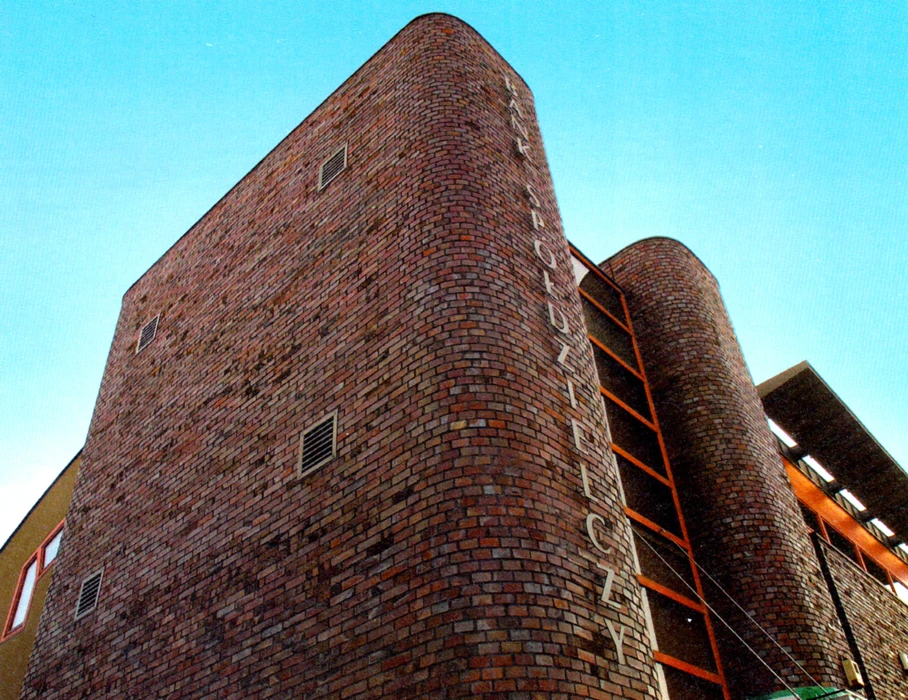
Klinkier schnie błyskawicznie
W średniowieczu cegłę suszono w suszarniach naturalnych, a czas suszenia cegły był długi i trwał od 4 do 5 tygodni. Aby zapewnić wolny proces wysychania i tym samym zmniejszyć naprężenia materiału podczas obsychania dużych gotyckich cegieł, suszący się materiał przykrywano słomą, później wilgotnym płótnem. Proces suszenia był żmudny, a cegła duża i ciężka. Ponadto naturalne suszarnie były uzależnione od warunków pogodowych.
Zupełnie inaczej jest dzisiaj, kiedy to suszenie w suszarniach tunelowych, rzadziej komorowych jest sterowane automatycznie i programowane w zależności od wyrobu i użytych podczas formowania dodatków.
Wielkość cegieł produkowanych w średniowieczu prawdopodobnie podyktowana była strukturą tego wyrobu, która była podobna do „pumeksu”. Ponieważ wyrób podczas formowania wymagał dodatku dużej ilości wody, należało domieszać do cegły składniki, które pomagałyby w jej odprowadzeniu podczas procesu suszenia. Najczęściej był to żużel. Sposób pakowania materiału po formowaniu i nierównomiernie przygotowana mieszanka wpływały na niższą odporność cegieł i przypadkową trwałość materiału. Z wadą tą poradzono sobie zwiększając wymiar cegły. Jednak produkcja wielkich bloków była ciężka i nie mogło być mowy o oszczędności materiału.
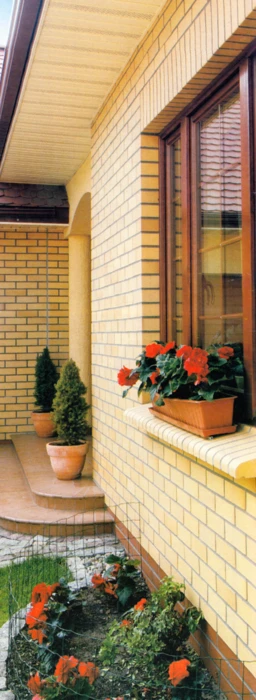
Obecnie produkowane wyroby o dużej trwałości, pełnej mrozoodporności, dobrym ujednorodnieniu masy, poprawnej strukturze formowania, mają dużo lepsze parametry techniczne.
Literatura podaje, iż wypał prowadzono w piecach podobnych do dzisiaj znanych pieców Hoffmana, przy znacznym zużyciu paliwa. Ówczesny proces wypału niczym nie przypominał dzisiejszego wysoko oszczędnego wypału w piecach tunelowych opalanych gazem ziemnym, w których pomiar temperatury na każdym etapie wypału jest mierzony i sterowany automatycznie. Obecne metody wypału dają możliwości dodatkowego wybarwiania cegieł. Proces wypału trwa od 2 do 3 dni. Gotowe cegły są rozsortowywane na palety i pakowane w zależności od przeznaczenia.
Pomimo to, że dzisiaj proces produkcji jest procesem wysoko zautomatyzowanym, to w technologii produkcji wykorzystywanej dawniej i dziś jest wiele elementów wspólnych, a producenci wytwarzający swoje wyroby nadal wykorzystują techniki używane dawniej, aby jeszcze bardziej wzbogacić wygląd estetyczny swoich wyrobów.
W artykule wykorzystano informacje historyczne zawarte w pracy Grzegorza Rogińskiego pt. „Manufaktura Ceglarska na Zamku w Gniewie”
mgr inż. Anna Wilk
Ceramika Budowlana
Wydanie Specjalne „Klinkier”